Как производят обувь на фабрике Юничел
27.06.2012
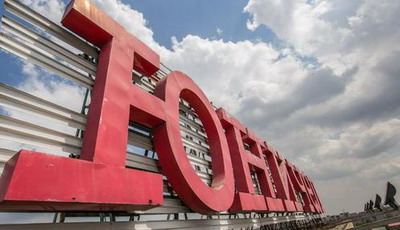
Очень интересный фото-обзор с анализом производственных мощностей одного из самых крупных российских производителей мужской и женской обуви,
фабрики Юничел. Приступим!
Юничел - фабрика мужской, женской и детской обуви, которая работает с 1932 года. Здесь существует очень много отделов и фабрика обеспечивает себя некоторыми очень важными комплектующими. но о всем более подробно.
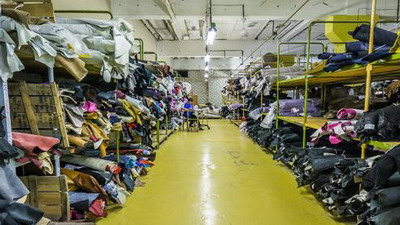
Первое, на что бросается глаз на фабрике - это склады с материалами. Это и кожа, и мех, и искусственные материалы. Кожа, которая поступает на фабрику тщательно проверяется. Кожа измеряется не вручную. На фабрике есть специальные устройства, которые определяют площадь каждого куска.
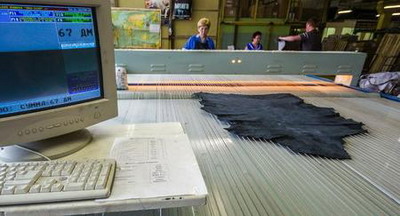
Аналогично все происходит и с фурнитурой. Каждая частичка будущей обуви проверяется вручную, и не выборочно - а вся.
Это позволяет предприятию избежать больших издержек на бракованный товар.
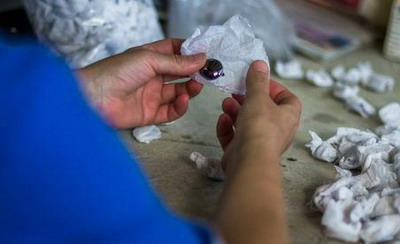
После проверки материалов, они поступают на другой склад - после которого попадут уже в производство.
Очень важным на обувном предприятии является отдел испытаний над обувью и лаборатории. Важно, чтобы на каждой фабрике были такие части производства. И на Юничел - это есть.
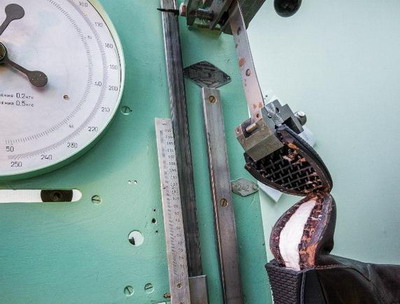
Первое, что попадается на глаза - это станок, который проверяет на прочность соединение подошвы с верхом обуви. Этот станок определяет с какой силой напряжением нужно приложиться к модели обуви, чтобы она вышла из носибельного состояния.
Второе - это проверка кожи на прочность и растяжение. Берется небольшой кусочек кожи (на фото он розовый), закладывается в пазы станка и растягивается. Здесь также определяют, какую силу нужно приложить к коже, чтобы она порвалась.
В этой испытательной лаборатории есть станок, который анализирует скорость и возможность износа обуви. В него закладываются несколько типов кожи, при включенном станке она начинает сгибаться в разных местах.

За одно включение станок проходит около 1000 циклов. А включают его для проверки одного куска кожи около 3-х раз. Это равносильно целому году интенсивного ношения такой обуви. Поэтому качество произведенной модели будет соответствующим.
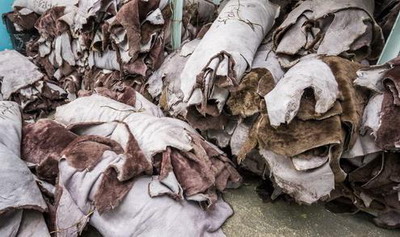
Проходя далее по фабрике, попадаем в раскройный отдел. Уже здесь начинается производство обуви. Здесь есть место хранения меха, кожи и других материалов.
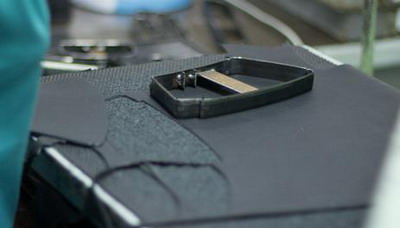
Для того, чтобы из кожи вырезать некоторый кусок для обуви используются специальные заостренные формы. Они под влиянием пресса вырезают нужную заготовку.
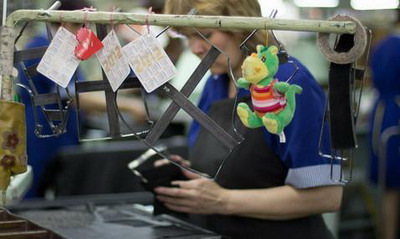
Каждый мастер, который работает в этом отделе имеет собственное рабочее место - здесь висят не только формы, который необходимы для вырезания, но и личные вещи каждого работника. Очень положительным фактором является и тип пресса, который при этом используется. Такой пресс запустить можно только тогда, когда Ваши обе руки лежат на кнопках. Соответственно, свои ценные для жизни руки Вы никогда, даже нечаянно, не положите под пресс.
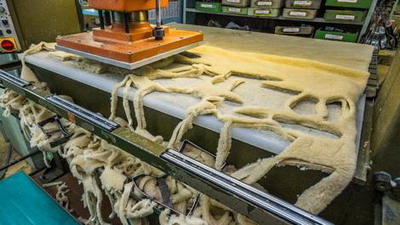
Аналогично таким прессам, есть станки, которые предназначены для вырезания меха. Они работают в автоматическом режиме. По словам работников этих цехов, только в начале работы (когда только вникаешь в суть дела) думаешь о том, как выгоднее использовать тот или иной кусок кожи и как разместить на нем максимальное количество деталей. А с опытом, эти процессы в голове происходят автоматически.
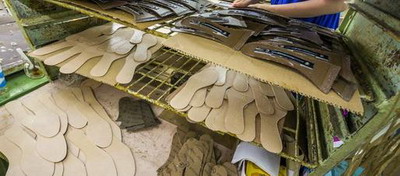
В следующем цеху делаются супинаторы для обуви. Сначала вырезаются картонные стельки, а потом к ним крепятся железные супинаторы. Это основа, которая будет удерживать каблук и основание обуви постоянно в одном и том же положении.
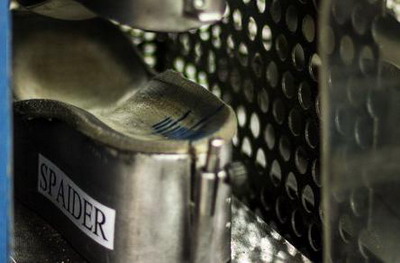
После создания супинатора на основе, к ней приклеивается плотная стелька и ставится также под специальный пресс, который создает из простой линии картонных склеек, отпечаток ступни. Такой отпечаток будет способствовать тому, что Ваша обувь будет ложится исключительно по Вашей ноге.
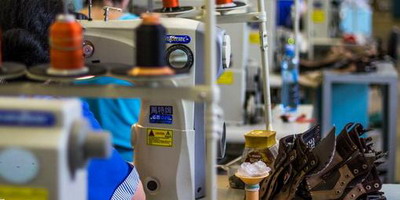
Следующий цех фабрики - это цех по пошиву верха обуви. Здесь будет прошиваться верх: от шнурков и заклепочек до змеек и резиночек. Работает цех по пошиву верха с конвеером (как свободного типа, так и принудительного).
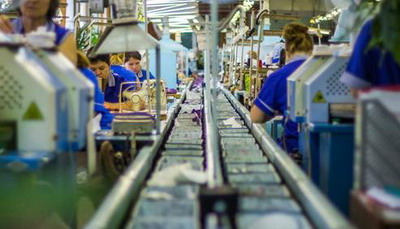
Здесь нужно полностью сшить все верхние части обуви. После чего, они передадутся в другой цех. В следующем цеху этот верх будет одеваться на специальную обувную колодку для придания обуви формы ноги.
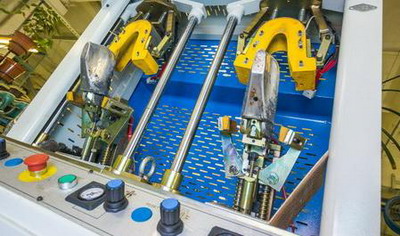
В таком цеху можно увидеть формовочный станок, который будет делать пятку обуви. Он влияет на материал верха таким образом, что после создания пяточной формы - она останется в течении носки обуви на своем месте.
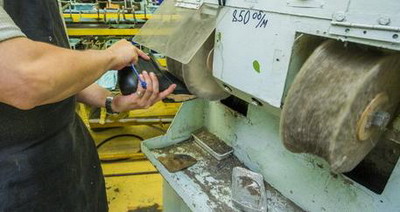
Когда обувь сформована, но требует дополнительной обработки - придания блеска или гладкости - то ее отправляют на специальный шлифовальный станок. На таком станке, мужские классические туфли превратятся из невзрачных с блестящие и начищенные.
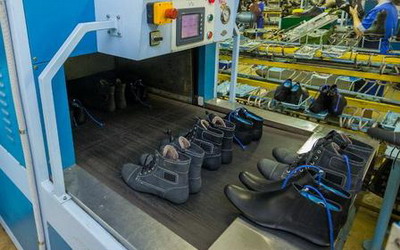
После того, как верх всей обуви уже готов - его отправляют в термо-станок, где обувь термически обрабатывается и "закаляется". Тепловая обработка способствует тому, чтобы обувь держала изначальную форму и в процессе носки не перекашивалась.
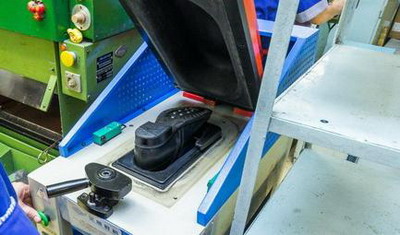
После этого, обувь готова к приклейке на нее подошвы. Это делается также с помощью пресса, который давлением на подошву и верх обуви делает отличный клейкий шов.
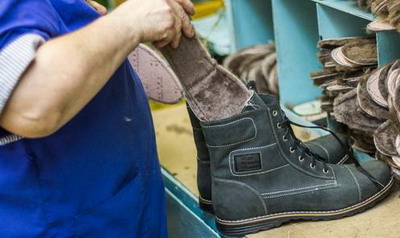
Следующий этап - это вкладка стелечки. Это, безусловно, ручной труд. Стелька ложится в обувь впритык и будет держать тепло в обуви.
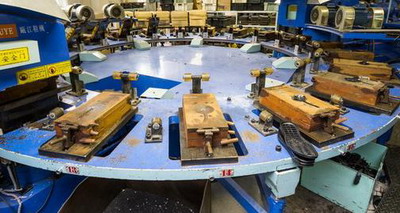
На фабрике Юничел есть также отдел, который занимается производством и литьем подошв. Для них используется специальный гранулированный порошок, который растапливается и из него выливаются подошвы определенного размера.
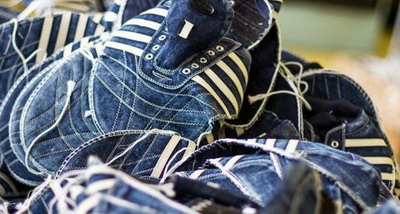
Среди обуви, которая производится на фабрике - есть обувь как с клеевой подошвой, так и с литой. Другими словами, верх обуви (как на рисунке), опускается в емкость с будущей подошвой. Таким образом, верх обуви как бы "вливается" в резиновую подошву.
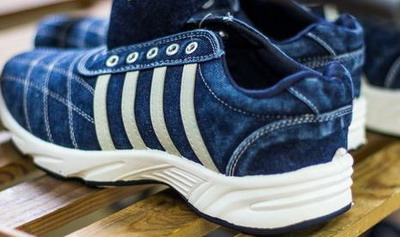
После этого процесса - получается вот такая моделька. Хоть и экономная по бюджету - но очень даже красивая и прочная.
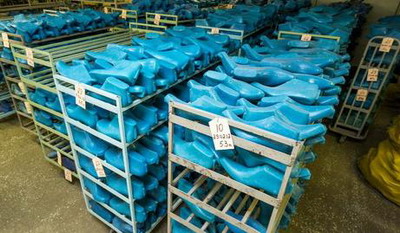
Особенностью фабрики Юничел является также и то, что данное предприятие само производит обувные колодки. Иногда, предприятие продает их для других предприятий. Но также использует и для своей обуви. Колодка - это имитация ноги человека, который будет носить данную модель. Ранее, на предприятии использовался материал красного цвета для колодок и поэтому колодки были красные. От них очень уставали глаза, поэтому было принято решение о замене цвета - и в Юничел синие колодки.
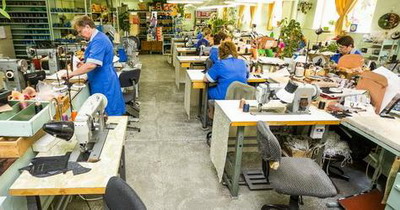
На фабрике есть особый отдел разработок. Здесь дизайнеры моделируют будущие коллекции, а самые первые мастера, работники с большим опытом и умельцы высочайшего уровня отшивают по 1-й модели каждого образца. Они определяют - как лучше производить модель при массовом производстве, определяют какие нужно делать детали и какие использовать материалы.
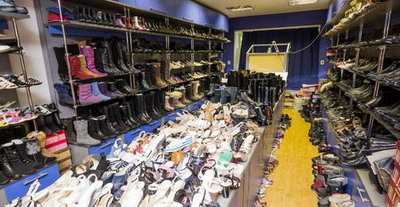
Каждая модель обуви, которая отшивалась в единственном экземпляре, попадает на отдельный склад. Он существует как для истории, так и для общей статистики предприятия. Вообще, процесс производства обуви очень тяжелый и не простой. Но тем не менее, предприятие Юничел отлично справляется с этим процессом и отшивает на своих 3-х фабриках около полтора миллиона пар обуви в год.
Это отнюдь не маленькие цифры. Но и фабрика, как Вы видите - организована очень успешно и хорошо. За работниками руководство очень хорошо следит - для них созданы все условия для защиты и безопасной работы, условия для отдыха (прекрасная столовая) и хорошее отношение.
Source: Обувное сердце страны
References to similar news
12.07.2013
В чем разница между дизайнерской и фабричной обувью?
Многие из нас сталкивались с вопросом: в чем же разница между обувью, которую шьют дизайнеры и между обувью, которая отшивается массово? Разница есть и кому что больше подходит рассмотрим...
09.10.2012
Совет производителю: как позаботиться об оптовиках
У производителей обуви главным клиентом - является оптовый покупатель, поэтому о нем нужно думать и заботиться. Как это сделать - проанализирует веб-каталог Обувь...
10.09.2010
Юничел подвергся вторжению вора, который украл 2 пары обуви
Ранним утром, пятого сентября, магазин «Юничел» на Жердева подвергся вторжению злоумышленника, который успел похитить лишь две пары обуви...
17.11.2005
Юничел. Производство обуви. Второе место в России.
По итогам 10 месяцев 2005 года Челябинская обувная фирма "Юничел" по объёмам производства обуви вышла на второе место в России, после Краснода
04.08.2005
ЗАО Юничел на 10,6 процента перевыполнило производственный план июля
ЗАО Юничел на 10,6 процента перевыполнило производственный план июля